Manufacturer Saved from Major Plant Failure
Customer Project
The customer manufactures a wide range of plastic storage containers for various applications. They experienced a major plant failure which led to a 50% loss of cooling duty from the site's own cooling systems. This had a major impact on the site's ability to maintain the production levels needed to serve its customers.
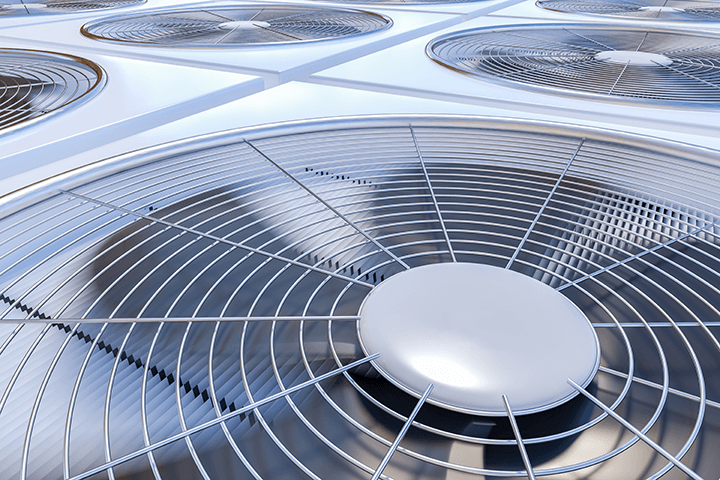
Action/Solution
The call was received from the client's site facilities team and we were on-site within a couple of hours to look at the issues. The existing chiller was beyond economic repair. A replacement was only available with a manufacturing lead time and would need to go through the company's capital expenditure approval first.
Having identified the machines that this chiller served, we found that the load on the chiller had increased over time. To accommodate this increased load, we selected a hire unit with 25% additional capacity but with a similar footprint and no increase in power supply. Some modifications were made to pipework to aid installation and future replacement which was arranged by the site's own in-house engineers, ready for our units arriving later in the day.
Outcome/Benefits
Our hire chiller and installation team arrived on-site within 10.5 hours of the original call and all affected machines were operational within 15 hours. This helped to minimise the loss of production into a recoverable position. The chiller was also sized to offer some redundancy as required.
In less than a day, DGPCC saved this manufacturer from major plant failure and a potentially significant loss of product and income.