Keeping Pharma Products Cool
Customer Project
A major pharmaceutical outsourcing company was experiencing ongoing issues with a critical part of their cooling plant. The unit in question was offering a nominal amount of cooling power, around 1.1MW of cooling capacity, and it was essential their pharma products were kept cool. Continuing maintenance issues were proving both disruptive and costly, and they found that a major overhaul was required which would need to be done offsite and would take several weeks.
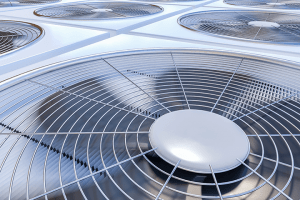
Action/Solution
We worked with the production, site services, and engineering teams to form a plan of action to replace the unit with minimum disruption to productivity. We arranged additional connection points, valves and electrical supplies so the existing unit could be run up until the last minute and a clean changeover could be performed over the next weekend. An area was chosen so there was no impact on the removal or replacement of existing equipment.
Outcome/Benefits
The customer had no downtime on production of their pharma products. The units offered some redundancy on existing plant and they were fully maintained during the hire period. The existing plant could be removed without issue and although the initial hire period was advised as 4-5 weeks for repairs, it transpired the original unit was beyond economic repair and a replacement was needed. Our flexible hire arrangement allowed them more time to design and order a new system suited to their future plans, including a power upgrade and other enabling works.